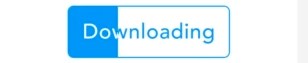


Diffusion rates are high leading to high shrinkage and densification. MIM parts are often sintered at temperatures nearly high enough to induce partial melting in a process termed liquid phase sintering. Sintering heats the powder to temperatures near the melting point in a protective atmosphere furnace to densify the particles using capillary forces in a process called sintering. To improve handling often the debinding and sintering are combined into a single process. The resulting, fragile and porous (40 volume percent "air") part, is in a condition called the "brown" stage. Next, a portion of the binder material is removed using solvent, thermal furnaces, catalytic process, or a combination of methods. The molded or "green part" is cooled and ejected from the mold. The process steps involve combining metal powders with polymers such as wax and polypropylene binders to produce the "feedstock" mix that is injected as a liquid into a mold using plastic injection molding machines. MIM technology improved cost efficiency through high volume production to "net-shape", negating costly, additional operations such as machining although MIM is weak in terms of tight dimensional specifications. MIM gained recognition throughout the 1990s as improvements to subsequent conditioning processes resulted in an end product that performs similarly to or better than those made through competing processes. Wiech later patented his process, and it was widely adopted for manufacturing use in the 1980s. in the 1970s, who refined MIM technology as co-founder of a California company named Parmatech, the name being condensed from the phrase "particle materials technology".
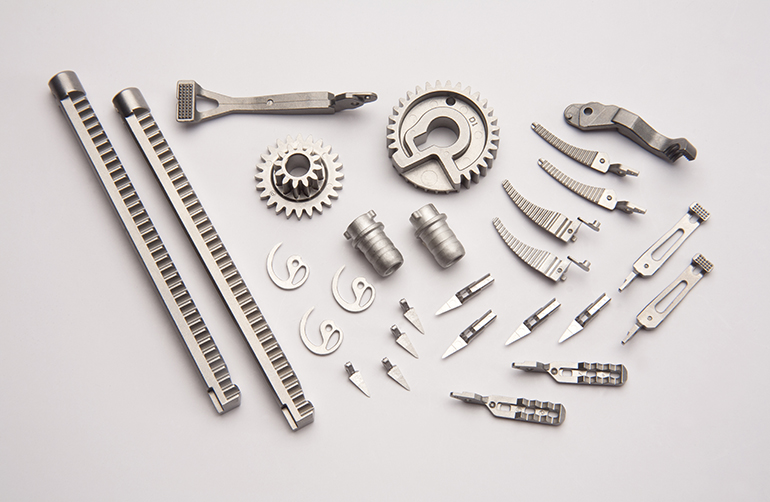
This indication of the possibility of MIM-casting, which was implemented by Dr.

Gribovsky, published in 1956, describes in detail the technology of hot casting (hot molding) ceramic products under pressure (now, Low Pressure Powder Injection Molding) and, in particular, notes that "hot casting technology provides the ability to manufacture products from any solid materials, ranging from natural minerals, pure oxides, carbides, metals, etc., and ending with multicomponent composite synthetic materials and their combinations". Įyeglass components produced by powder injection molding Most of the growth in recent years has been in Asia. A related technology is ceramic powder injection molding, leading to about US$2 billion total sales. The metal injection molding market has grown from US$9 million in 1986, to US$382 million in 2004 to more than US$1.5 billion in 2015. The latter operation typically shrinks the product by 15% in each dimension. After the initial molding, the feedstock binder is removed, and the metal particles are diffusion bonded and densified to achieve the desired strength properties. MIM feedstock can be composed of a plethora of metals, but most common are stainless steels, widely used in powder metallurgy. This shot can be distributed into multiple cavities, making MIM cost-effective for small, intricate, high-volume products, which would otherwise be expensive to produce. The behavior of MIM feedstock is governed by rheology, the study of sludges, suspensions, and other non-Newtonian fluids.ĭue to current equipment limitations, products must be molded using quantities of 100 grams or less per "shot" into the mold. Finished products are small components used in many industries and applications. After molding, the part undergoes conditioning operations to remove the binder (debinding) and densify the powders. The molding process allows high volume, complex parts to be shaped in a single step. Metal injection molding ( MIM) is a metalworking process in which finely-powdered metal is mixed with binder material to create a "feedstock" that is then shaped and solidified using injection molding. Metal parts produced by injection molding
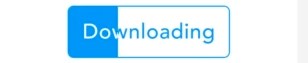